Polyurethane elastomers - Technologies
Key properties of polyurethane elastomers
Polyurethanes are materials that, like rubber, belong to the elastomer group. They are obtained by reacting isocyanates with polyalcohols. In the subsequent reaction, chain elongation takes place, resulting in flexible materials with the desired mechanical strength and wear resistance. The qualitative and quantitative selection of the constituent substances and the possibility of using appropriate additives makes it possible to obtain a wide range of products that are better in many respects rubber product substitute.
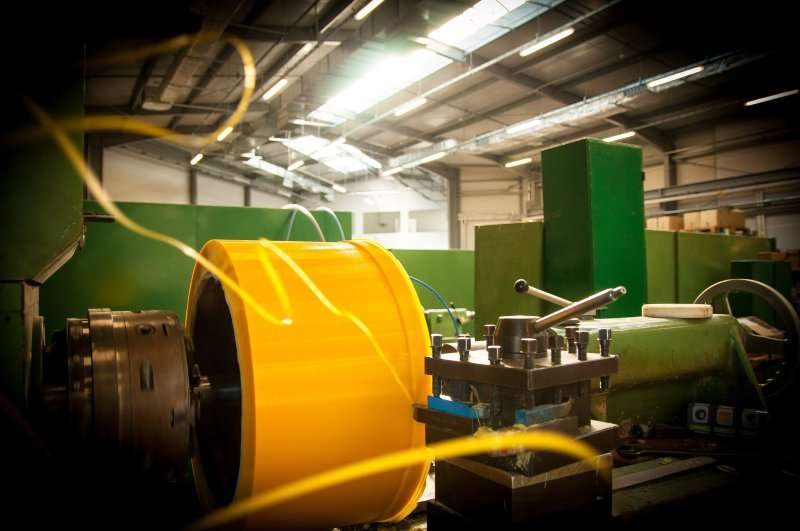
Turning
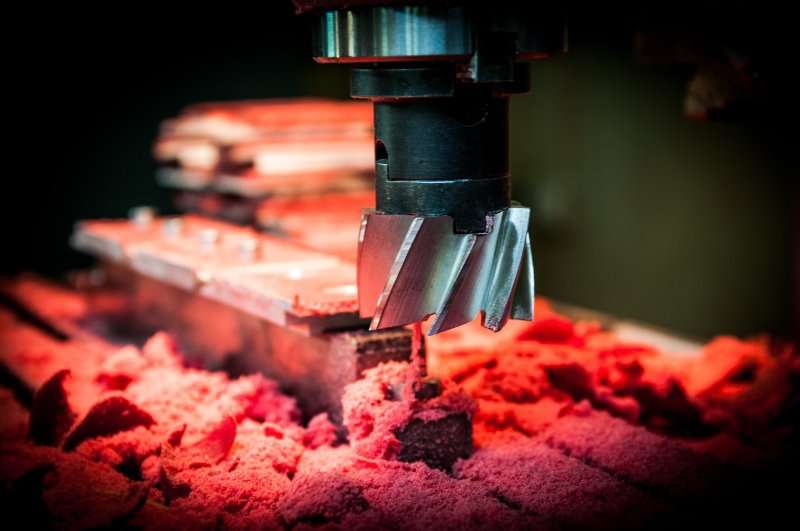
Milling
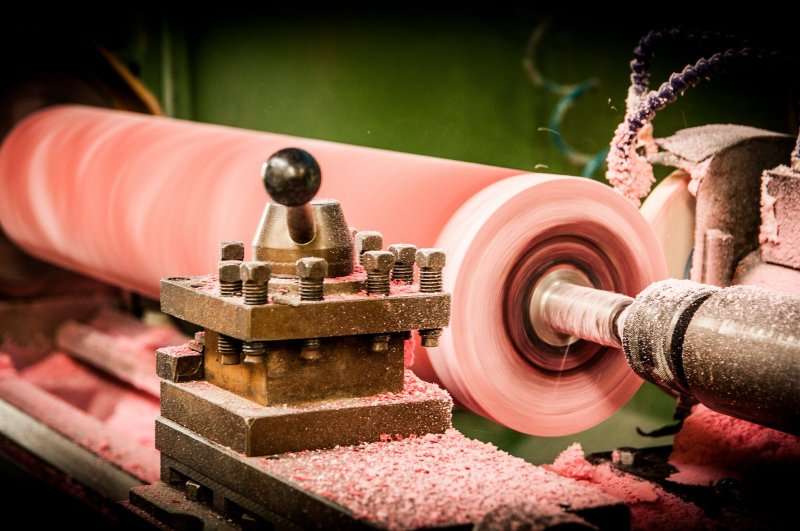
Grinding
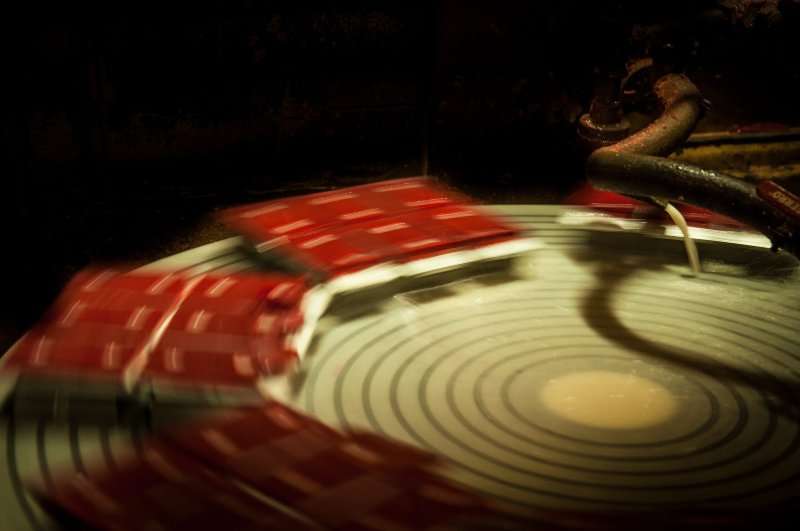
Horizontal grinding
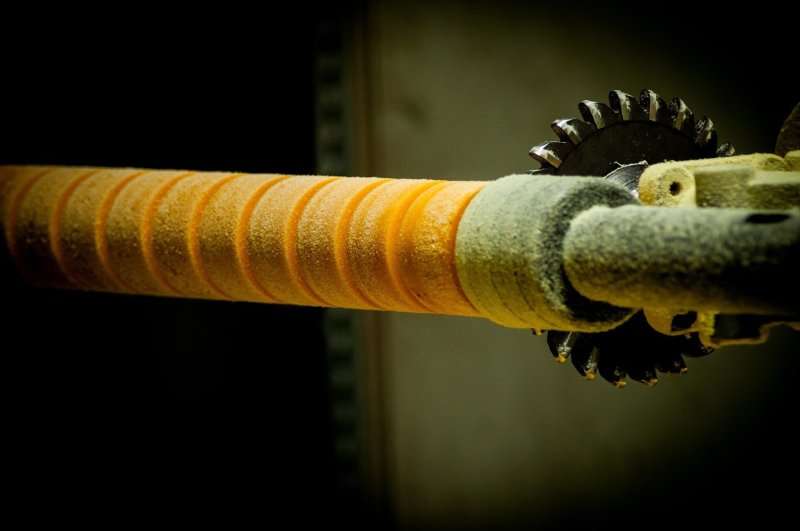
Grooving
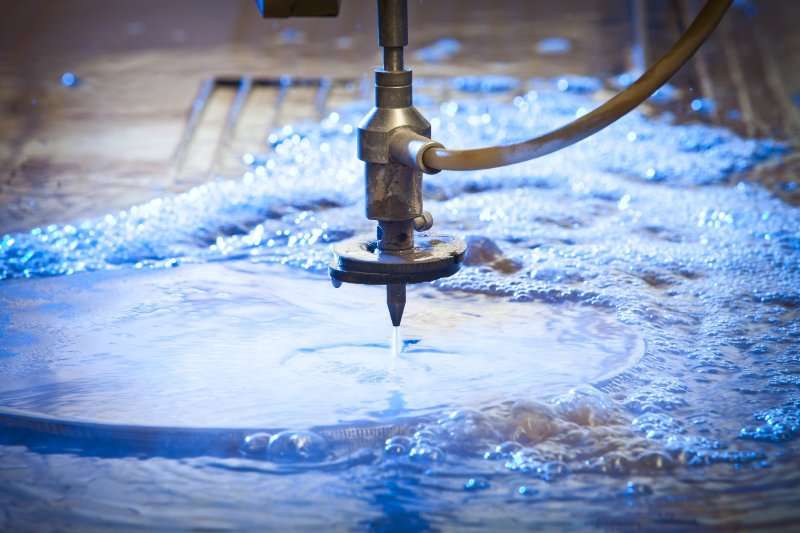
Waterjet cutting
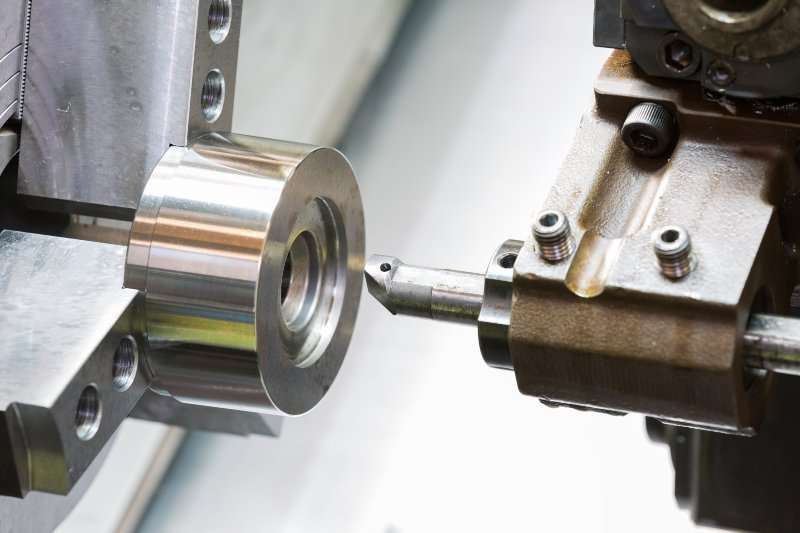
Manufacture of metal moulds and components
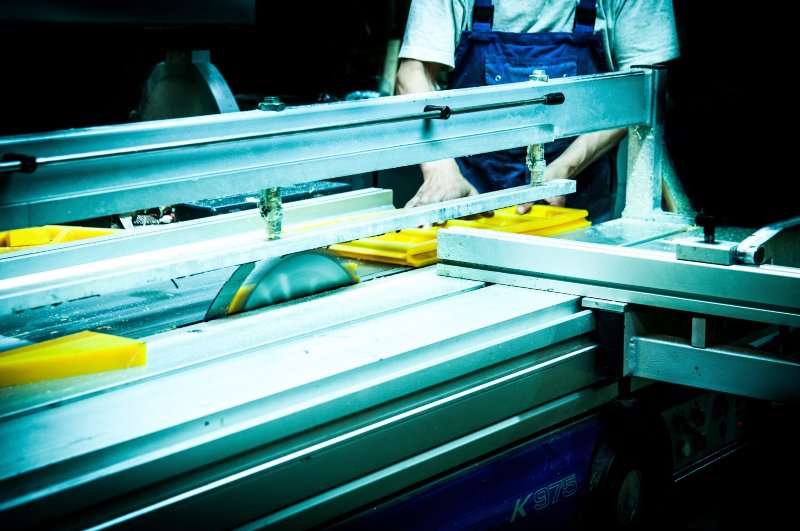
Saw cutting
THIS TYPE OF MATERIAL HAS A NUMBER OF ADVANTAGES THAT ARE USED IN MANY AREAS OF MODERN INDUSTRY. EACH POLYURETHANE ELASTOMER IS CHARACTERISED BY:
- high resistance to abrasion, cutting and tearing,
- high elongation at break,
- good damping and high energy absorption capacity,
- high elasticity in a wide range of hardnesses,
- resistance to ageing of the material, exposure to agents
- atmospheric, light, UV radiation and ozone,
- good resistance to mineral oils, petrol, acids, alkalis, alcohols and many other chemicals,
- good adhesion to metals and other materials,
- resistance to micro-organisms,
- the possibility of imparting antistatic properties
Asmaprene A
Components manufactured from this system show excellent cut resistance, and are also characterised by resistance to mechanical agents and chemicals - oils, greases and solvents.
- Characteristics: High-quality polyurethane system for pouring with good physical properties.
- Application: The best system for components requiring high cut resistance.
- Benefits: Excellent physical properties, high tensile and tear resistance.
- Resilience: Very good resistance to oils, greases, alcohols and hydrocarbon solvents.
- Operating temperature: Continuous operation in dry environment up to 80oC, short-term operation in dry environment up to 100oC. Long-term operation in a water environment up to 50oC.
- Range of available hardnesses: System available in hardnesses from 70.80 to 93 ShA
Asmaprene B
A system with a smaller hardness range (greater component flexibility), good resistance to grease and oils and solvents.
- Characteristics: System for pouring in smaller hardness ranges.
- Benefits: Excellent flexibility and elasticity, excellent adhesion to metal, low degree of deformation over time.
- Resilience: Very good resistance to mineral oils, greases and solvents, not resistant to hydrolysis.
- Operating temperatures: Continuous operation in dry environments up to 60oC, short-term up to 80oC.
- Range of available hardnesses: Asmaprene B is available in hardnesses from 25 to 60 ShA
Asmaprene BE
A system characterised by high mechanical properties, good abrasion resistance and elasticity of products in a wide range of hardnesses.
- Characteristics: Polyurethane system with very good mechanical properties. Excellent elasticity and resilience over a wide range of hardnesses.
- Applications: Roll coverings, technical components requiring abrasion resistance in the lower hardness ranges, as well as good cut resistance.
- Benefits: Very good mechanical properties. High abrasion resistance. High flexibility, excellent adhesion to metal, carbon fibre and fibreglass.
- Resilience: Very high resistance to mineral oils and greases. Minimal swelling in contact with solvents. Not resistant to hydrolysis.
- Operating temperatures: Continuous operation in dry environments up to 80oC, short-term up to 100oC.
- Range of available hardnesses: In a hardness range of 40 to 80 ShA.
- Notes: The main application is in the hardness range from 50 to 70 ShA, as components with these hardness parameters have very good wear resistance with a relatively soft surface.
Asmaprene L
High-quality system characterised by good strength parameters while resisting hydrolysis.
- Applications: Coatings for heavy-duty applications, e.g. shafts for heavy industry, especially when working in humid environments (contact with water and high temperatures).
- Benefits: Excellent durability, resistance to hydrolysis, high rebound, excellent adhesion to metal, polyamide, fibreglass, carbon fibre, low abrasion.
- Resilience: Good resistance to oils and greases. Very good resistance to hydrolysis. Resistance to micro-organisms.
- Temperatures: continuous operation 60 to 80oC in dry and humid environments, short-term operation up to 100oC (dry and humid operating averages).
- Range of available hardnesses: From 70 ShA to 95 ShA and 60 ShD and 75 ShD
Asmaprene Q
A polyurethane system developed for applications requiring the highest abrasion resistance found mainly in the mining industry. A system that fulfils all the tasks required of screens, ensuring the highest product quality.
- Characteristics: A polyurethane system developed for applications requiring the highest abrasion resistance and used mainly in the mining industry. It is additionally characterised by enhanced dynamic properties.
- Application: Great for screens and applications requiring high abrasion and tear resistance.
- Benefits: Particularly low abrasion, good mechanical and dynamic properties, high resistance to cutting
- Resilience: Possibility of giving antibacterial, anti-static properties.
- Hardnesses available: system available in hardnesses from 55 to 95 ShA
Amaprene C
High-performance polyurethane system for the manufacture of highly stressed, fast-wearing components requiring resistance to hydrolysis or micro-organisms.
- Applications: Fast-wearing rollers (e.g. in carbon fibre production), wheels for industrial applications. Ideally suited for screens and seals.
- Benefits: Very high strength properties over a large hardness range. High resistance to yellowing under UV light, and the formula can be modified to suit special requirements.
- Resilience: Good resistance to greases, fats, hydrocarbon solvents (e.g. toluene, heptane, ethyl acetate), alcohols (e.g. propylene glycol). Antistatic, antibacterial additives can be used.
- Operating temperature: Continuous operation in wet environment up to 60oC, dry environment up to 80oC. Short term operation in contact with solvents up to 100oC.
- Range of available hardnesses: 50 to 95 Sh A
- Notes: Can be used briefly in contact with food (dry and wet).
Vulkollan
A polyurethane system used in the manufacture of components operating in harsh environments, especially those exposed to high dynamic loads.
- Characteristics: Components manufactured from this system have excellent strength properties. The oldest and best developed system formulation, sold exclusively by Bayer.
- Application: For use in wheel and shaft linings operating under severe operating conditions, subjected to dynamic loads, as well as in the manufacture of spring elements or couplings where resistance to abrasion and a low coefficient of friction are required.
- Properties: High dynamic load capacity, excellent mechanical properties over a wide temperature range, excellent abrasion resistance, low coefficient of friction, high fatigue strength, low strain rate over long operating times, constant e-modulus in the temperature range from - 20oC to + 80oC, excellent adhesion to metal. Very high resistance to mineral greases and oils, minimal swelling in glycol, no resistance to hydrolysis or microorganisms.
- Operating temperature: Continuous operation in dry environments up to 100oC, short-term up to 120oC. Maintains excellent properties at low temperatures down to - 20oC.
- Range of available hardnesses: 65 to 93 ShA
Asmathane
A polyurethane system with good fatigue resistance and a good value for money.
- Applications: Abrasion-resistant coatings, mechanically stressed polyurethane details.
- Benefits: Very good abrasion resistance, good mechanical properties with good elasticity. Good resistance to ageing by UV light (low yellowing).
- Resilience: Very good resistance to mineral grease and fats, good resistance to solvents used in cement production. Special microbial-resistant formulation possible.
- Operating temperature: Continuous operation in dry environments from -30 to 60 oC, briefly up to 80oC
- Range of available hardnesses: 50 to 90 ShA
Pouring of polyurethane - Rubberising
Asma Polska specialises in polyurethane pouring technology, commonly referred to as rubberising. This process, although seemingly complicated, thanks to our experience and production capacity, is carried out quickly and precisely.
Pouring polyurethane is an innovative method of protecting various types of surface against mechanical damage, chemicals or corrosion. By using high-quality polyurethane, which is characterised by extraordinary mechanical and chemical strength or the ability to bear heavy loads, we create a highly resistant coating.
Depending on our customers' needs, we can customise the hardness, thickness and colour of the rubberisation. Our process allows polyurethane to be applied to a variety of materials such as plastics, metals, aluminium.
It rubberises:
- shafts
- rolls
- sleeves
- sheet metal,
- snow groomer stars
and many other technical parts.
Polyurethane is a rubber-like material hence the name rubberisation. Rubberised rollers show better wear resistance. Rubberised rollers have much better anti-slip properties. Rubberised plates absorb noise and do not corrode as much as before protection.
In a nutshell, the gumming process at Asma Polska is as follows:
- First, the old worn elastomeric coating must be separated from the technical part.
- Such a coating is removed either mechanically or chemically.
- The part must then be sandblasted, poprimed and moulded.
- We coat the moulded part with polyurethane by gravity.
We look forward to working with you.
We know as little about gumming as anyone!
Below are examples of substances to which polyurethane is resistant. You can obtain detailed information by contacting our employees.
- Acetylene
- Ethyl alcohol
- Methyl alcohol
- Ink, ink
- Ammonium nitrate
- Lead nitrate
- Silver nitrate
- Petrol, petroleum ether
- Bitumen
- Borax
- Butane
- Copper chloride
- Nickel chloride
- Potassium chloride
- Mercuric chloride
- Mercury
- Ammonium sulphate
- Copper sulphate
- Nickel sulphate 10%
- NaCl aqueous solution
- Ether
- Dimethyl ether
- Phenylethyl ether
- Isopropyl ether
- Ethylene
- Sodium phosphate, aqueous solution
- Glycerine
- Diethylene glycol
- Glucose
- Hexane
- Glue
- Cresols
- Boric acid 10%
- Oleic acid
- Potassium sulphate
- Sodium sulphate 10%
- Iron sulphate
- Carbonic acid
- Fatty acids
- Butter
- Milk
- Lead acetate, aqueous solution
- Cotton oil
- Coconut oil
- Castor oil
- Spruce oil
- Mineral oils
- Vegetable oils
- Paraffin
- Beer
- Propane
- Crude oil
- Barium salts
- Copper salts 10%
- Nickel salts 10%
Versatile polyurethane elastomers
Due to the ability to shape the properties of polyurethane elastomers to a very large extent, they can be used in many industries. They are effectively displacing traditional materials such as rubber or silicone from the market. They are much lighter than metal and absorb vibrations much better than other plastics. Importantly, polyurethane elastomers perform successfully in both wet and dry conditions. Thanks to their excellent technical parameters and processing capabilities, polyurethane elastomers can be used successfully in the engineering, mining, paper, wood, food, agricultural, automotive and many other industries. Thanks to the possibility of intervening in the chemical composition, we are able to create a material with predictable parameters adapted to specific expectations.
It produces primarily from polyurethane elastomers:
- Wheels and castors
- Rod bushings and rings
- Technical seals
- Panels and claddings
- Slides and tracks
- Nozzles and hydrocyclones
- Polyurethane screens
- Positioning elements
- Pulleys and scrapers for conveyor belts
- Bumpers and anti-vibration and bumper elements
- Caterpillar machine components
- Screw conveyors
- Pipeline cleaning components
- Clutch inserts
- And many other bespoke products
In recent years, there has been a noticeable increase in the use of polyurethane elastomers in further areas of the economy.
Thanks to the knowledge we have acquired, our state-of-the-art machinery and our many years of experience in the plastics processing industry, we offer polyurethane products of the highest quality, at attractive prices and with realistic lead times.
We look forward to working with you.
Asma Polska - production and reconditioning of technical parts made of polyurethane
Asma Poland is:
We perfectly understand that customer satisfaction is the driving force behind the stable development of our company. Our individual approach to each and every customer, regardless of the size and value of the order, has already led to us being trusted by more than five thousand companies at home and abroad. We would like to thank you for the trust you have placed in us and we believe that in the years to come, more and more companies will appreciate the quality we offer.
When we started our business, our products were mainly sold on the Polish market. Since then, we have managed to gain the trust of many foreign companies. Today, more than 80% of our production is addressed to customers from North America, South America, Asia and most of Eastern and Western Europe. Continuous acquisition of new customers and expansion into new markets is an integral part of our company policy.
The high quality of our products and services is our top priority. Our quality control department has advanced measuring equipment and every employee in our company is committed to quality policy. In order to meet the quality requirements of our customers, we have developed a number of advanced procedures. All departments and processes in our company and our suppliers are subject to control. At present, the complaint level is < 1%.
Do you need help?
Click the "CONTACT" button, fill in and send the application form. We will contact you within one working day.